Think slip clutches for soft starts
A slip clutch in a medical device can avoid sudden starts and stops that might jar delicate devices or solutions.
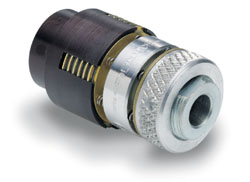
The clutch with friction pads slips at a break-away torque, and gives a constant continuous torque at this setting until the impediment is removed. A basic mechanism uses axial-loaded plates and friction pads to transmit torque.
A slip clutch can often solve motion problems for medical-equipment designers at a lower cost and while lasting longer than alternate methods. For example, in the automation of medical manufacturing, slip clutches provide soft starts for machines, protect mechanisms from overload, and control material tension on labeling equipment, among other tasks.
In general, slip clutches have torques that range from oz-in. to over 1,000 lb-in. (Other clutches are used to engage and disengage mechanisms and also for overload protection.) Slip-clutch capacity is dependent on torque, rpm, and duty cycle, and a reduction in any of these parameters causes a subsequent increase in any other. The clutch's capacity limit is based on heat buildup calculated with:
P = 0.011T
Where P = power, W; T = torque, in.-lb; and = speed, rpm
As expected, excess heat shortens clutch life.
For overload protection, a slip clutch can be anything from a simple shear pin, to a ball detent, to a more complex device with friction pads.
A shear pin works only once to save a mechanism from damage. The pin then needs replacing. A ball detent, a simple mechanical assembly, slips at the set torque, with a pulsating torque going from zero to the break-away setting. Remove the obstruction and the device again functions for overload protection. Clutches with friction pads slip at the break-away torque, and give a constant continuous torque at this setting until the impediment is removed. A basic mechanism uses axial-loaded plates and friction pads to transmit torque. The higher the axial load, the higher the torque.
The axial load can be supplied mechanically by springs or electrically. In the latter case, changing the torque is a matter of varying the voltage. Servomechanisms can also vary torque to the needs of the equipment. This simplifies set up because changes can be dialed-in and repeated as needed. Well-designed friction systems have a long life of 30 million cycles and provide accurate repeatable torques. In most cases, slip clutches outlast the mechanism they are in.
Slip clutches with a static friction lower than their dynamic friction ensure torque is gradually applied. This means, for instance, that the tension on paper as it gets rolled on spools in labeling equipment is also gradually applied.
This kind of tension control is accurate, repeatable, cushioned, and durable. Machines can run faster without overloading material and also with less impact on gears, pulleys, and chains.
Interestingly, tension control also increases tool life. Capping machines are a good example. They use elastomer wheels to screw caps onto bottles as they move along a packaging line. In an old design, when a cap bottomed-out, the wheels would slip against a cap, damaging them and the bottle. In a newer design, in which slippage is taken up by the clutch, the wheels stop when the cap is screwed all the way on. Similar applications automate the closing of valves, setting of controls, and the turning of screws to a certain torque.
Slip clutches also can be used for the low-speed indexing of controls, tables, conveyors, and similar devices, with overload protection obtained for “free.” For instance, a simple index mechanism consists of a hook or hold that catches a pin attached to an index wheel. The clutch slips until a solenoid pulls the hold away, which frees the wheel to turn. The solenoid then returns the hold to its initial position before the next pin arrives. This arrangement allows a single or a partial revolution which users can easily change by moving pins. Even programming uneven indexes is simple: Just move the pins to unequally spaced positions.
To generate a controlled pushing force, let a slipping clutch push against a connecting force arm. A transported product on a conveyor pushes against a gate without damage to the product or conveyor because all slippage is in the clutch. It's also possible to generate pushing force by combining a slip clutch with a rack and pinion, belt, or chain. Torque control in these cases can be either tension or thrust control.
Of course, slip clutches can also be used in any application where a temporary stoppage comes from just holding the mechanism. Think of how a pastry display case in a restaurant rotates slowly until a patron gently holds the case. Slip clutches let moving mechanisms such as slides, tables, and conveyors stop temporarily in a similar fashion. The clutches are also useful at the end of a cycle when a motor moves a mechanism into a locked position, such as with a linear motor stop. Instead of having a time delay to keep the motor from burning up, a slip clutch can do the job for any length of time.
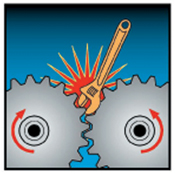
A slip clutch in the gear shafts keeps dropped items from jamming and overloading a mechanism.
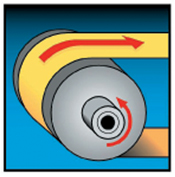
Slip clutches allow the gradual application of torque and thereby cushion suddenly applied loads. The tension on the paper going around a roller on a packaging mechanism is thus also gradually applied. The machine can run faster without overloading the material.
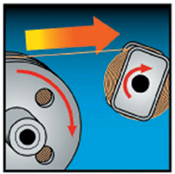
The cushioning effect of a slip clutch acts throughout a machine and reduces shock on gears, pulleys, and slides.
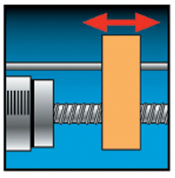
A linear positioning mechanism with a slip clutch produces soft starts and cushioned stops.
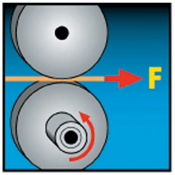
A slip clutch can also limit tension on material passing between two rollers.
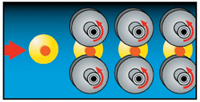
On a capping machine, a slip clutch stops the elastomer wheels (grey wheels) from turning once the cap is screwed all the way onto a bottle.
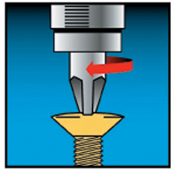
Turning a screw to a preset torque is controlled with a pneumatically actuated slip clutch.
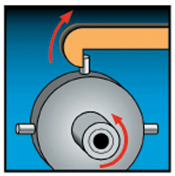
A simple index mechanism consists of a hold or a hook that catches a pin on an index wheel. The clutch slips until a solenoid pulls the hold away, which frees the wheel to turn.
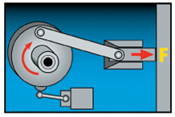
A controlled pushing force is generated when a slipping clutch pushes against a connecting force arm.
Want to use this article? Click here for options!
© 2008 Penton Media Inc.
Webcasts
-
Supercharging Products with Embedded RFID
Sponsored by: Skyetek -
Discovering Direct Metal Laser Sintering for Faster Rapid Prototyping
Sponsored by: Morris Technologies -
Wireless Sensor Networks-A Survey of Design Optics
Sponsored by: Winland Electronics, Inc. -
Gearmotors: Achieving The Perfect Match
Sponsored by: Groschopp - View Webcast Archive
Latest in Blogs
Leslie Gordon - "From Shop Floor to Software"